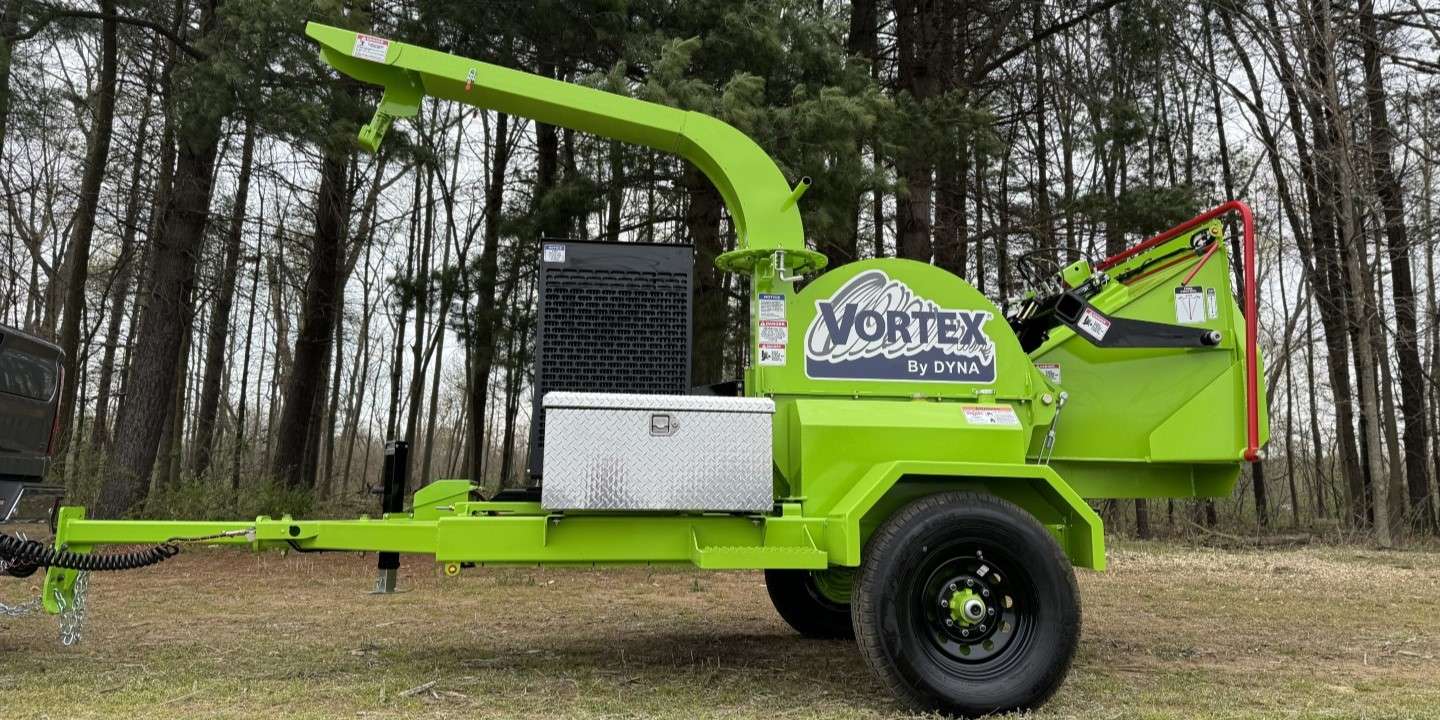
VORTEX V12-31
Wood Chipper
- Patented Vortex Chamber
- 44-inch discharge impeller
- Reverse Pivot Feed System
- 12 inch by 32 inch Opening
- Hand Fed or Machine Fed
- KDI Diesel and Gas Options
Because of the design characteristics of the patented VORTEX® chamber, the V12-31 has more capacity than any other chipper in the 12 inch class. While most chippers in this class have openings 12 inches high and from 15 inches to 20 inches wide, the VORTEX® V12-31 has an opening of 12 inches high by 32 inches wide …. 50% to 100% bigger. This makes it suitable for multiple markets others can’t handle. Tree care, municipalities, utility line maintenance, golf course management, and even light land clearing are all better suited to the VORTEX® V12-31 than others in its class.
Hand fed or machine fed, the “oversized” opening makes feeding and operating best in class. While operators of other brands must “cut to the opening”, VORTEX® V12-31 operators can process limbs, branches, and even small whole trees as-is, bringing truth to the statement of “less trim time” that others claim.
Add in the revolutionary skinless-no pocket drum, you have the highest capacity, most productive machine in the 12-inch class available in today’s market.
Because of the design characteristics of the patented VORTEX® chamber, the V12-31 has more capacity than any other chipper in the 12 inch class. While most chippers in this class have openings 12 inches high and from 15 inches to 20 inches wide, the VORTEX® V12-31 has an opening of 12 inches high by 32 inches wide …. 50% to 100% bigger. This makes it suitable for multiple markets others can’t handle. Tree care, municipalities, utility line maintenance, golf course management, and even light land clearing are all better suited to the VORTEX® V12-31 than others in its class.
Hand fed or machine fed, the “oversized” opening makes feeding and operating best in class. While operators of other brands must “cut to the opening”, VORTEX® V12-31 operators can process limbs, branches, and even small whole trees as-is, bringing truth to the statement of “less trim time” that others claim.
Add in the revolutionary skinless-no pocket drum, you have the highest capacity, most productive machine in the 12-inch class available in today’s market.
Just as brush chippers are classified or ranked on chipping capacity by the linear height of their feed opening, there is also more to the numbers associated with drum diameter, drum speed, and engine horsepower when determining the true performance of a machine. One has to examine how that engine horsepower is utilized across its rotational components. Bigger is not always better.
Put A Better Spin On It
The VORTEX® chipping system separates and isolates the functions of chipping and throwing to each take full advantage of the maximum available horsepower and torque delivered from the engine in their own individual way. In a conventional drum system where the drum is bound to both chipping an throwing functions along the same rim diameter, torque/power from the engine is surrendered at the expense of having to spin the drum faster to adequately throw chips, especially if the drum is “oversized”. Rotational cutting force at the knife tip increases the closer you get to the axis of the drum. With a “right-sized” drum where the diameter and RPM are not physically tied to throwing capability, less horsepower and less fuel are required to generate a greater cutting force at the knife tip. Mounted independently along the same shaft of drum in the patented VORTEX® chamber, the disc-shaped impeller will have increased leverage, inertia (flywheel effect), and rim speed for throwing.
Separation of chipping and throwing functions for better performance
The VORTEX® design offers a more dialed-in drum chipping ability with segregated throwing mechanics. Benefits include better use of engine horsepower/torque, faster engine recovery times during auto-feed stops, and better overall performance when it comes to both chipping and throwing. A VORTEX® chipper naturally and positively chips like a drum, and throws like a disc — allowing operators to experience the “best of both worlds” in one machine.
Until the introduction of the revolutionary VORTEX® chipping system, all drum chippers, as we know, have a “pocket” in the surface of the drum to carry chips to the discharge port. This is not the optimum means of throwing chips nor does it make for the most durable weldment, or even lend itself to ease of serviceability. Because the VORTEX® chipping system separates the chip throwing responsibility to an attached impeller to the drum shaft, the pocketless/skinless VORTEX® drum itself will make several gains in its abilities to chip when cutting is its primary, isolated function.
A New Spin
Without having to “carry out” a throwing operation, the VORTEX® drum is not dependent upon the minimum requirements needed by the drum in order to achieve acceptable throwing capability and avoid plugging, in terms of RPMs and size. Thus, it is easier to maintain ideal drum speeds, with more torque delivered to a “right-sized” diameter drum from the engine instead of having to operate at higher, torque-robbing RPMs because of the need to throw. Since cutting force at the knife tip increases the closer you get to the axis of the drum, reducing both the drum diameter and the drum RPM creates a greater cutting force at the knife tip. Plugging is virtually a non-factor due to the speed relationship between the drum and discharge disc, and recovery time is quickened between auto feed stops. Overall, the VORTEX® chipping system is able to match these most favorable conditions with its drum configuration and properties.
The VORTEX® “no-pocket” drum with throwing impeller (disc)
Look Ma … No Pockets
The VORTEX® pocketless/skinless drum creates no restrictions on chip flow after a chip comes off the knife. Chips immediately fall into the cone-shaped bellypan where they are pushed as well as pulled by gravity and air to the discharge fan. No pockets are needed to carry chips. Drums with pockets do not allow for interior welding of the drum skin or much of the interior of the pocket and knife holder. Over a period of time, chipping stress causes welds to give way and knife holders to break away, which are both dangerous and expensive to repair. Because the VORTEX® drum has no exterior surface “skin”, the entire interior of the drum as well as the knife holders are fully exposed. This open face allows 100% weld coverage on all drum components making for a far superior and more durable assembly.
Open and exposed access to knife holders
Gain Access
The open and exposed access to knife holders, allow for added weld coverage making knife support stronger and allows knife bolts to be fastened with wrench-accessible backside nuts; no more threaded holders.
A more durable assembly with 100% weld coverage
A VORTEX® chipper has a feed system that offers the best aligned mechanical leverage of any other feed system. A reverse pivot feed system creates its own leverage by gravity and the rotation of the feed wheel at the yoke arm “wrist” joint. Together with its wider opening and broad infeed hopper, limby and/or bulky materials are compressed over a larger area and are naturally pushed, not pulled, into the machine. This results in less trimming and stoppages of workflow to reposition branches.
Feed Off Physics
By using proper angles of the yoke arms, the extra large diameter single feed wheel is able to climb up onto wood and create down pressure to crush as well as natural mechanical leverage to feed material to the drum. This system does not require excessive springs or additional hydraulic assist cylinders meaning fewer moving parts, less maintenance, less trimming, and reduced cleanup time. Limbs, branches, and trees are virtually pushed into the chipper without the need for a bottom feed wheel. Never again will you have to unthaw or dislodge branches from a frozen or jammed bottom feed wheel; or clean up the mess below when its trap door is left open. One hydraulic motor powers the feed system, controlled by the wrap-around control bar, where feeding rates are tuned to deliver the best synchronized, torque-crested cutting ability of the drum.
VORTEX® Reverse Pivot Feed System
In a predominantly “copy-cat” industry, the patented VORTEX® chamber is the key structural design technology that sets it apart from all previous approaches used to design and construct a drum-style brush chipper. The VORTEX® chipper challenges the question of how machines should really cut and throw, while offering many other performance advantages within this unique compartment, which make it all possible.
Go With The Flow
The VORTEX® chamber is an enclosed, semi-cone shaped area that acts as the bellypan where chips are guided and accelerated into the discharge paddles. Unlike conventional drum chambers that tightly wrap the drum, the VORTEX® chamber is open and is progressively tapered wider toward the discharge housing. This allows both gravity and powerful air currents generated by the spinning drum and impeller assembly to create a unrestricted pathway for chips to naturally flow directly toward the discharge paddles. Conventional drum-style chippers require the drum to carry the chips in pockets around to the back of drum where they are then released at the rim-speed of the drum itself. As soon as a chip comes off of the knife on the drum in the VORTEX® chamber, that chip is instantly drawn into the disc-shaped discharge impeller where it can be thrust with the rim-speed of the disc, which is nearly twice the rim-speed of the drum.
The patented VORTEX® chamber
Speak Volumes
Due to the high volume of air generated within the VORTEX® chamber, many added benefits are available to the operator aside from the ability to cut brush consistently and move chips with unparalleled velocity. Plugging is practically impossible. There is no place for the chips to accumulate because the discharge paddles are always throwing faster than the drum knives are chipping, even under a larger load. Plus, the amount of unidirectional airflow forcing material to exit the discharge is tremendous. This airflow also controls dust and “blowback”, the chipping residue that is cast back through the feed system onto the infeed pan or ground more commonly observed with traditional drum-style chippers. The VORTEX® chamber also allows for a screen to be placed to size material into a consistent, uniform valued-added product, such as micro-chips to meet customer demands.
The progressively tapered chamber guides chips to the discharge housing
What if you could enjoy the chip cutting benefits of a drum chipper while also having the the chip throwing capability of a disc chipper? It is seldom argued in the tree care industry that a traditional disc-style chipper can throw chips faster and farther than any traditional drum-style chipper. Yet a traditional drum chipper has its advantages processing bulky material but at the expense of lesser chip throwing velocity. With the introduction of the revolutionary VORTEX® chipping system, you can now have the best of both worlds.
Know Your Role
Cutting and throwing are two separate functions, each requiring a separate set of physics in order to be performed at peak efficiency. In a traditional drum-style chipper, the drum itself is solely responsible for combining both of these processes. However, there is a notable difference in the desired rotational speed of the drum to utilize the most torque for the drum to cut versus the minimum rotational speed required for the drum to throw. For throwing, there are “pockets” built into the surface of traditional drums to carry chips to the discharge port. These pockets demand higher RPM, sacrificing torque needed for cutting, to achieve the speed needed to propel the chips out of the drum chamber with sufficient velocity to exit the discharge without plugging. Plus, pockets allow chips to ricochet within during their move to the discharge, robbing them of the velocity and proper direction needed to discharge most effectively.
Throw chips faster and farther
A Drum To Cut, A Disc To Throw
When it comes to chipping and throwing functions with a VORTEX® chipper, there is a separation of these concerns. A “no-pocket” drum is mounted to a disc-shaped impeller, or rotor, that is nearly twice the diameter of the drum. Together, this assembly rotates within the patented VORTEX® chamber, a semi-cone shaped housing that acts as a bellypan where chips are guided and accelerated into the discharge paddles of the impeller naturally by gravity and forces it creates. This design allows the drum to maintain maximum cutting force and optimum RPM for cutting while the impeller (the disc) gains amplified rim speed, transferred from the shaft to its larger diameter for throwing.
The VORTEX® “no-pocket” drum and impeller (disc) assembly
Get Wind Of This
Within the patented VORTEX® chamber, chips naturally flow unencumbered from one side to the other without added mechanical means once the chips fall from the knife and pass the anvil. Gravity and centrifugal forces pull chips away from the drum and toward the fan paddles on the discharge disc, where they are swiped and accelerated in an unrestricted manner toward the exit of the machine. The discharge paddles follow a greater arc and therefore a faster outer tip speed than that of the drum. This not only creates a dramatic increase in velocity for launching the chips, but it also virtually eliminates plugging. There is no place for the chips to accumulate because the disc is always spinning faster and throwing faster than the drum is chipping. By removing the burden of throwing chips from the drum and using a separate device for the sole purpose of throwing, the flow of chips also does not have to endure collisions within angled transitions and discharge chutes on traditional drum-style chippers. This also allows the operator to select any of the 360 degrees for positioning the discharge to throw chips in any direction without impact on performance. The result is a tremendous throwing ability that outpaces and outdistances any other machine in its class.
No angled transition or chute to create collisions along the discharge pathway
A Breath Of Fresh Air
The ability of a brush chipper to discharge wood chips can impact your performance and image. Having direct and precise throwing ability not only allows you to pack trailers fuller, but also helps minimize the mess on a customer job site. When the engine bogs down, slowing the rate of the drum, the VORTEX® discharge system can still thrust chips with velocity, which helps avoid scattered piles of driveled chips at the base of the machine. Also, the amount of “blowback” is practically eliminated because the suction and wind velocity generated within the chipping chamber pulls chips back into the chipper rather than pitching them out the pan and onto the ground. Cleanup will be faster and easier. Plus, having added reach and distance when choosing where to deposit chips because of the VORTEX® effect on throwing ability can have its advantages.
When tree care professionals are asked about the size of opening they’d prefer, the answer is always the same — as big as possible. The VORTEX® design allows the drum to be considerably wider, twice as wide in most cases, than drums that are currently on the market. Spanning the full width of a drum, the VORTEX® opening is nearly, in every case, twice as wide as all others in its class. The math is simple – the larger the opening, the more material can be placed into the chipper at one time for processing.
A Battle Of Widths
When limby trees or brush are compressed by a chipper’s feed system, it will naturally tend to expand horizontally as it is weighted by the feed wheel (like a baker’s rolling pin). Having a smaller, less-width, more square-shaped opening can create more contact, abrasion, and resistance during feeding as material is forced to rigidly compress horizontally by the left and right sidewalls of the opening in addition to vertically from the feed wheel. This can lead to more trimming and stoppages of workflow to reposition a branches. The VORTEX® design will always allow for much wider openings because its openings are not as limited proportionally by the maximum construction extents of a disc or drum size. Therefore, a wider spanning rectangular opening will be far more receptive to incoming material, allowing more volume to pass unimpeded through the opening and feed system en route to the cutting drum.
The opening of a VORTEX® chipper spans up to twice the width of all others in its class … no restrictions due to drum size and disc weight constraints.
Squares and Inches
The tree care industry often recognizes chipper capacity as being classified by one standard linear measurement of the height of a chipper’s feed opening (12″, 15″, 18″). However it is more revealing to use two dimensions instead of one in order to calculate the area of the opening to more accurately determine how much material volume the chipper can actually accept. One could refer to this as the target area for feeding. A wider opening offers more “space” for densely packed brush and limbs as they are funneled into the machine.
A comparison of various opening sizes from various chippers makes (drawn to scale). Which would you prefer to feed?
Open Wide
As mentioned, wider openings can eliminate trimming, but there are also other benefits. The wider opening creates a wider angle of entry possible for incoming material, aiding in curbside operations or keeping operators further to the side of the machine. A wider opening creates more width for the feed system to compress and “pancake” material to be rolled into the chipper, which helps process bulky/bundled materials like pine, palm fronds, shrub prunings, or other fibrous species. A wider opening can also make feeding with a mechanical loader much more efficient, providing a larger target to place a limb to get it started.
Engine | Kohler 74 HP KDI Diesel or 133 HP PSI Gas |
---|---|
Cutting Drum | 16″ diameter x 30″ long, open face, no pockets |
Discharge Impeller | 44″ diameter x 3/8″ thick |
Feed Wheel | (1) 13″ diameter x 31″ wide, reverse pivot system |
Throat Opening | 31″ wide by 12″ high |
Axle | 7,000 lb. Torflex |
Tires | ST235/80/R16 6-ply mounted on 8-bolt rim |
Hitch | Pintle Ring |
Paint | Painted with PPG safety fluorescent green |
Weight | 6,400 lbs |
Vortex No Pocket Drum
Patented Vortex Chamber
44-inch discharge impeller
Reverse Pivot Feed System
12 inch by 32 inch Opening
Hand Fed or Machine Fed
KDI Diesel and Gas Options
Hydraulic Winch
Bump Bar Tailgate
Brush Buddy Pusher Kit
Traffic Cone Kit
Spare Tire Kit
In Feed Curtain Kit